How does clinching work?
You may already have heard of clinching as a mechanical interlock connection process, or a cold welding process.
Clinching requires only the sheet metals to be assembled. No consumables such as rivets, glue, screws or welding are needed to assemble the metal parts.
During the clinching process, the metal sheets are plastically deformed. A special punch and die causes the creation of the interlock between the sheet metal layers.
The punch is moved with the required force depending on the thickness and the strength of the materials to be joined and the die is fixed.
Deformation of the sheets by compression between punch and die:
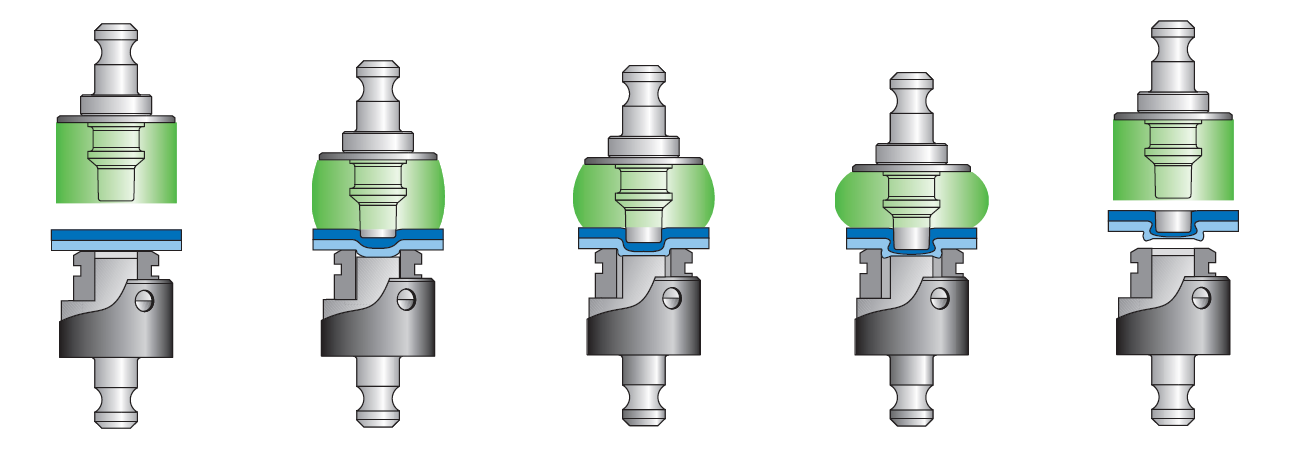
1) After being placed, the materials to be joined are firstly forced into the die with the punch.
2) As soon as the lowest material is resting on the die anvil, it starts flowing sideways under the pressure being exerted by the punch. The blades are pushed outwards.
3) The punch is then returned to its starting position by the operator or by a pneumatic timer which removes the force.
4) The metal sheets are now joined and can be removed. The blades are pulled back together by a spring.
5) The result is a resistant clinch joint.
A classic RIVCLINCH® clinch joint is created in less than a second. Depending on materials and conditions it can reach 100 to 300ms.
There is absolutely no specific skills required to use our clinching equipment. It is actually very fast and simple to clinch.
The RIVCLINCH® joining system may be adapted to existing presses or used in custom-built machines. Both single points and multiple points can be set at the same time. An integration of the clinching system into manual machines, robots and stationary tools is feasible.
Clinching is used to join steel and stainless steel materials as well as aluminium and other non-ferrous materials in a cost-effective and environmentally friendly manner.